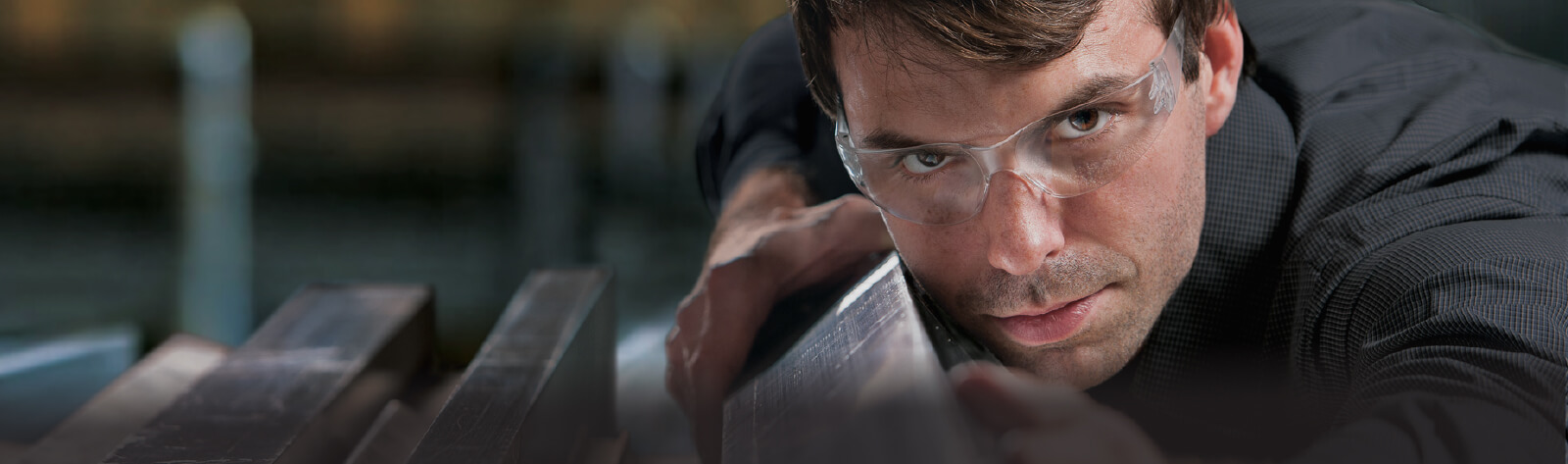
DRT 201
FAQs
Using the DRT-201 Drying Rate test device
- How is the fabric sample secured to the plate in the AATCC Test Method 201 (TM201)?
- The test method indicates that a single hold-down strip be used on the upwind edge. We have found that blue painters tape works well for this purpose. We are also aware of clients using double-stick tape affixed to the heated plate. The sample can be stuck directly to this surface, only replacing the tape when it loses adhesion strength. If the test sample has any type of curling or lifting behavior, we recommend adding tape to the two downwind corners (at minimum) or fully taping all sides of the sample in place. The samples should be installed with no stretch, but adding a tiny amount of tension during the taping process will typically result in more repeatable behavior.
- Can you apply this test to socks? When you cut the specimen, it rolls and will not be in full contact with the plate.
- This is a tricky application, and not currently addressed in the TM201 standard. Sample results can vary significantly if the wetted area has inconsistent contact with the hotplate surface. If taping the edges of the sample do not result in consistent contact, then a hold-down mechanism will be needed. One example of this is described in ISO 11092, AnnexC and consists of a metal frame with wires mounted in one direction to have minimal interference on airflow. If a finer hold-down grid is required, you can experiment with wire mesh, although this will have a larger disruption to the airflow. Using a pre-made cooling rack for baked goods would be a low-cost way to experiment with this hold-down method. If you are using any type of surface hold-down, you should use it consistently across all samples for comparative results.
- Does the device need to be placed in a conditioned lab?
- To comply with the AATCC TM201 requirements, lab environment must be maintained at 21 +/- 2 °C, 65 +/- 5% RH for textiles. The test can be performed in any stable environment for internal comparative testing, but for any published results or comparison with other labs, the environment should be maintained within the stated limits.
- Does the heat generation from the device disrupt the conditioned lab environment?
- The DRT-201 drying rate test device generates only a small heat load (nominally 40W), and will not impact conditioned spaces or actively controlled climate chambers.
- Why do some data sets have a temperature increase spike right as the water is delivered?
- When operating the device, is it quite common to see a temperature increase as the water is dispensed beneath the fabric. This is a normal behavior and does not impact the computation of drying time or rate. The plate is controlled to 37 °C and environment typically maintained at 21 °C. This results in the surface of the sample reaching an equilibrium value between these two values. The greater the insulation, or Rc, of the samples, the cooler the measured surface temperature during initial conditioning. At the time of dispense, water which has been preheated by the plate wicks up into the sample resulting in a warm spot until evaporation kicks in. Smaller effects that contribute to this behavior include the water layer reducing contact resistance with the hotplate, and heat of sorption as fibers are wetted. Both of these are minor compared to the impact of warm water into the fabric.
- Are larger water volumes acceptable? What is the impact of larger volumes on drying time?
- Larger or smaller water volumes can be used if necessary to get consistent results. The drying time can be expected to vary directly with water volume. Twice the volume will take approximately twice as long to dry out. The reasons for adjusting the water volume typically relate to reliable sample wetting and surface cooling. If a sample has a large internal volume, additional water may be helpful to get a cooling effect on the surface. If the water volume wicks out to the edge of the sample, then the volume should be reduced. Volume used should always be reported and only like volumes used for comparison between samples.
- When is a textile considered “thick” and might require special considerations with this device?
- Sample thickness can affect results in two areas: disrupting airflow and limiting surface cooling. The Thermetrics DRT-201 includes the ability to adjust the height of the heated plate. It is recommended that for any sample greater than 1mm thick that the plate be adjusted to maintain the 1.0 +/- 0.1 cm distance between the sample and the thermocouple sensor. Some samples may be too thick and hydrophobic to exhibit any cooling at the fabric surface and cannot be tested with this method. Increasing the water dispense volume may improve measurement consistency. We recommend always staying with the preset 0.2 ml water delivery unless that is demonstrated to not be enough.
- Are there standard verification materials/results to verify the equipment works correctly? Is there a library of response curves and test results available for different specimen types?
- The development of the AATCC Test Method 201 included measurement of a series of samples to establish precision limits for the test method. This is the only currently published information about standard materials and results. There is an effort currently underway to perform round-robin testing on a series of materials and identify potential verification samples. This work is likely to conclude in the latter part of 2021.
The Drying Rate Standard and the Science
- Do you apply the fluid on the face or back of the specimen?
- The fluid is delivered on the back of the specimen at the contact interface between the heated plate and the sample. This mimics the interface between skin perspiration and garment contact.
- Is the small quantity of water chosen to ensure that evaporation is taking place at the fabric/plate interface?
- The water volume was selected based on early-stage testing to develop the instrument and standard. Too much water takes a long time to dry and can wick out to the sample edges, potentially disrupting the test. Too little may not generate a sufficient cooling event at the sample surface. The actual location of evaporation (heated plate interface vs surface of the sample) will vary based on sample construction and properties. It’s reasonable to assume that wherever water exists on, in, or under the sample, there will be some evaporation.
- How does the movement of air over the sample make a difference?
- The boundary layer is a critical factor for device repeatability and reproducibility. The convective heat transfer coefficient, hc, is primarily a function of air velocity and turbulence. Higher air movement results in a lower hc, which results in faster drying of the sample. Thermetrics has put a lot of focus on DRT-201 airflow tuning and control to keep results consistent between samples and across instruments.
- Does the hotplate temperature vary from 37 °C during the test?
- The hotplate is controlled to the operator setpoint (typically 37 °C) for the entire test interval. A PID algorithm modulates the heater power to maintain the surface temperate very precisely at the desired setpoint. While this is not physiologically realistic (human skin would cool down in this scenario), the instrument is designed per the test method to keep the plate temperature constant.
- Is the fabric cooler at the end of the test?
- In an ideal test, the fabric temperature should return to the same level as prior to dispensing fluid. After the water has fully evaporated, the before/after conditions are identical, and temperature should match also. But it is quite typical for the post-dryout temperature to be lower than starting temperature. This usually indicates the fabric has dimensionally changed and is not contacting the heated plate in the same manner as the start of test. Small wrinkles or shifts in the fabric can create air pockets under the fabric that cause the IR thermocouple above the fabric to measure a lower surface temperature. Careful attention to sample mounting and hold-down strategies can minimize this behavior.
- Can we do this same test with a sweating guarded hotplate?
- Not directly. Since sweating guarded hotplates typically have a water supply from multiple locations over the heated plate, it is not possible to precisely deliver a small volume to the center of the sample. With some modifications to the hotplate fluid supply and adding an IR thermocouple over the sample, similar results could be obtained, but it would not likely be fully compliant with AATCC TM201.
- Are the slides and video available from the webinar?
- If you didn’t receive the materials from our DRT webinar, visit our website at www.thermetrics.com or contact our sales team. We can get you set up.
Interpreting the Fabric Drying Rate Results
- How does this test relate to comfort?
- To our knowledge, test results from this method have not been formally correlated to wearer comfort. However, there is a significant body of research about the impact of skin wettedness on thermal comfort. Skin wettedness also has adverse consequences increasing the friction coefficient between garments and skin surfaces and creating physical discomfort.
- What are your findings to what makes a difference when applying this method to the same sample size? Absorbency? Wickability?
- This is a particularly challenging question, since the behaviors are interrelated. Water that spreads out to a larger surface area typically has a faster drying rate due to the larger available surface area for evaporation. Samples that absorb into tight internal pore structure can take longer to dry.
- Are there any advantages of using this method over AATCC 199 or AATCC 200?
- All three test methods (199, 200, 201) use some combination of heat and/or airflow to quantify drying behavior – but they are all different. TM199 exposes a fully saturated sample to a 37 °C environment and estimates dryout time based on weight loss. TM200 tests samples at several saturation levels including max absorbent capacity, but uses no external heating and estimates dryout time based on change in surface temperature while air is being drawn through the sample. TM201 uses a heated plate under the fabric, airflow across the top of the fabric, and it also estimates dryout time based on surface temperature. The advantage of TM201 is the more application-realistic heating/airflow configuration and how the water is delivered as a finite volume source at the fabric center also incorporates wicking performance into the measurement.
- How does this compare to the WATson test?
- The mechanism of this test is very similar to the WATson test. In both cases, the sample is in contact with a heated plate, begins in the dry state, has water injected beneath the sample, and then runs until the sample dries out again. The differences are that the WATson test uses the applied power to the heated plate (per sweating guarded hotplate methodology) as an indication of drying behavior, vs the DRT-201 which uses the surface temperature of the test specimen to detect drying. The WATson method uses a controlled delivery rate from a network of four pores until the sample is presumed saturated. The DRT-201 drying rate test device delivers a precise small volume to a single pore. The WATson protocol and instrument is considerably more complex, but the two protocols are similar in basic physics. Because of the similarity, it could be expected that both methods would order-rank samples in a comparable way. Thanks for this question – it is a good motivator for us to do a more extensive correlation study between the two methods.